Basic Knowledge of Magnetic Particle Crack Detection
Background
During the production of steel (casting), during the processing (rolling, forging, welding) and also during the utilization of steel components (bending and tensile loads) cracks can occur. Most often the crack formation begins at the surface and then the crack grows into the material due to stress concentrations at the crack tip. Finally, this can lead to a fatigue fracture of the component.
Therefore cracks are the most crucial defect type and must be eliminated by grinding out the crack or scrapping the complete component. The most sensitive method for the detection of surface cracks in ferromagnetic parts is magnetic particle crack testing method (MT) – also known as magnetic particle testing or fluxing for short.
The main applications are:
- Safety parts in automotive engineering (steering, axle and engine parts in forged, cast or machined finished condition)
- Welds on pressure vessels and pipelines
Advantages of magnetic particle crack detection
- Highest sensitivity for surface cracks, even with complicated workpiece geometry and unmachined surface
- Clear, reproducible crack indications
- Detection of hidden cracks just below the surface
- No special radiation protection regulations needs to be observed
- No special demands on the experience and skill of the inspectors, but rather on their due diligence and unfailing attention
Principle
Magnetic particle testing of magnetizable metals (mostly steel, less often nickel or cobalt), is well acknowledged by experts as a very reliable method. For inspection, the part needs to be magnetized. Large workpieces, for which complete magnetization is not possible, are magnetized only in the partial areas to be tested.
The field lines resulting from the magnetization run parallel to the surface within the component. Cracks that lie transverse to the field lines disturb them and thus generate a stray magnetic field or also called leakage flux.
This means that the field lines emerge from the ferromagnetic material on one side of the defect and re-enter on the other side. This results in the formation of magnetic poles. If iron powder is now spread over this stray field, it accumulates at the defect because it is attracted by the magnetic poles. Cracks that run in parallel to the field lines do not generate a stray field and therefore cannot be detected. Hidden cracks below the surface can only be located up to a certain depth (approx. 1 mm).
The processes for magnetization of workpieces are roughly divided into field and current flow. The application of both flow methods in one test cycle is also called combined magnetization.
Testing in detail
Field flow: If a component is exposed to a magnetic field, usually in a longitudinal direction, this is referred to as field flow. With the help of one or more current-carrying coils, a magnetic field is generated in a U-shaped iron yoke. The workpiece is clamped in this iron yoke. This creates a magnetic field in the longitudinal direction of the component. Cracks at right angles to this, so-called transverse cracks, form a flux leakage and are displayed.
Current flow: Depending on the test task, however, cracks in the longitudinal direction of the component need to be detected as well. For this a second kind of magnetization is used, the so-called current flow. During the current flow, an electrical current passes through the workpiece to be tested generating a ring-shaped magnetic field. This allows longitudinal cracks to be displayed on the test specimen.
Combined magnetization: For many components there is no bound crack orientation. Therefore, a preferred direction can not be expected. In the case of large quantities, for example for vehicle construction, testing takes place on testing machines. They allow field and current flow, which can be activated individually or combined (both simultaneously), so cracks of any orientation can be detected.
Testing agent: During magnetization, the fluorescent magnetic particles are applied. In most cases, this is done by wetting with an aqueous suspension. The fine particles, often these are ferromagnetic iron oxides, stick to the emerging magnetic fields. In order to increase the displayability, the particles are mixed with a fluorescent dye that glows yellowish-green under ultraviolet light (UV light). In a darkened room, this compound creates a luminous, high-contrast (crack) display, as a result of which even the finest imperfections can be identified.
Further Information
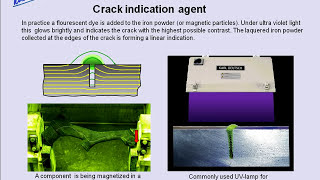
Further, comprehensive information on magnetic powder crack testing can be found in our knowledge floater video “Magnetic Particle Testing”.